Traffic Works Packaging
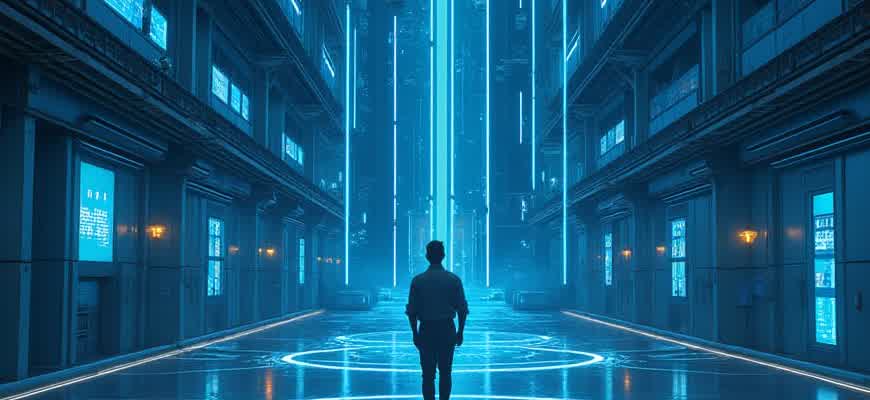
The packaging of traffic control products plays a critical role in ensuring both the safety and efficiency of roadworks. A well-designed package not only protects materials from damage but also facilitates easy storage, transport, and handling. Proper packaging is essential for maintaining the integrity of items such as cones, barriers, and signage throughout their lifecycle.
Key considerations in traffic works packaging include:
- Durability: Ensuring that the packaging is robust enough to withstand rough handling during transport.
- Visibility: Packaging should be designed to make the products easily identifiable at a glance.
- Eco-friendliness: Use of recyclable and sustainable materials is increasingly becoming a priority.
- Efficiency in Storage: Optimizing the space usage in storage facilities and on-site.
When evaluating different packaging options, companies should focus on minimizing waste while maximizing product safety. Below is a table summarizing different types of packaging materials used in traffic control items:
Material Type | Advantages | Disadvantages |
---|---|---|
Cardboard | Lightweight, recyclable, cost-effective | Less durable, susceptible to moisture damage |
Plastic | Waterproof, durable, reusable | Not biodegradable, higher cost |
Wooden Crates | Sturdy, reusable, secure | Heavy, expensive, not space-efficient |
Properly designed packaging ensures that traffic control materials remain in optimal condition, which directly impacts their effectiveness on the job site.
Choosing the Right Packaging Materials for Optimal Protection
When it comes to packaging for transportation and storage, selecting the right materials is essential to ensure product safety and integrity. Poor packaging choices can lead to damage, increased costs, and customer dissatisfaction. The right materials not only protect against physical damage but also help maintain the quality and appearance of the product during transit.
Different products require specific packaging solutions depending on their size, fragility, and susceptibility to external conditions such as moisture or temperature. Understanding these requirements and matching them with appropriate materials is crucial for optimizing protection and minimizing waste.
Factors to Consider When Choosing Packaging Materials
- Product Type: Fragile or delicate items need cushioning materials like foam or bubble wrap, while sturdy products can be packaged using cardboard or stretch film.
- Protection from Environmental Factors: Some items, such as electronics or food products, may require materials that protect from moisture, light, or temperature changes.
- Cost-Effectiveness: Consider both the cost of the materials and the potential for product damage. A more expensive material may prevent costly damage in the long run.
- Environmental Impact: Opting for recyclable or biodegradable packaging materials can contribute to sustainability efforts and align with eco-friendly business practices.
Types of Packaging Materials and Their Uses
Material | Best For | Advantages |
---|---|---|
Bubble Wrap | Fragile items like glass or electronics | Shock absorption, cushioning, lightweight |
Cardboard | General packaging, large items | Durable, customizable, recyclable |
Foam Inserts | Small, delicate products (e.g., jewelry, high-tech gadgets) | Excellent cushioning, precision fit |
Stretch Film | Palletized goods, large shipments | Secure, versatile, weather-resistant |
Choosing the right packaging material goes beyond cost. It’s about ensuring the safety of your product while maintaining environmental responsibility.
Ensuring Compliance with Safety Standards in Packaging
Compliance with safety regulations in packaging is a critical component in reducing risk during transport and storage. Packaging not only serves as a protective barrier for products but also ensures that goods comply with industry-specific safety standards, preventing potential hazards. Understanding these requirements is essential for manufacturers and logistics companies to guarantee the safe delivery of goods to their final destinations.
Various industries, such as pharmaceuticals, chemicals, and electronics, face unique safety challenges. Therefore, it is important to adhere to both local and international packaging standards, ensuring the safe handling of materials throughout the entire supply chain. Failing to meet these standards can result in penalties, product damage, or even harm to consumers.
Key Requirements for Safe Packaging Compliance
- Material Selection: Packaging materials must be suitable for the type of product being shipped, ensuring no chemical reactions or degradation occur during transport.
- Labeling: All packaging must include appropriate safety warnings, handling instructions, and compliance labels, ensuring that products are handled correctly at every stage.
- Packaging Integrity: The packaging must be durable enough to withstand environmental conditions like humidity, temperature variations, and physical stress.
Manufacturers must implement proper testing and validation procedures to confirm that packaging meets safety requirements. The following steps outline the process:
- Risk Assessment: Evaluate potential hazards associated with the product and determine appropriate packaging solutions.
- Material Testing: Test materials for durability, resistance, and compatibility with the product.
- Certification: Obtain the necessary certifications from regulatory bodies to ensure that packaging meets the required safety standards.
"Proper safety compliance not only protects products but also ensures the well-being of consumers, reducing the chances of accidents and product recalls."
Overview of Packaging Safety Regulations
Regulation | Industry | Requirement |
---|---|---|
UN 3480 | Chemicals | Specific packaging and labeling for hazardous goods |
ISO 11607 | Pharmaceuticals | Packaging must maintain sterility and product integrity |
ASTM D4169 | General | Packaging must withstand various shipping hazards |
Streamlining Inventory Management with Packaging Innovations
Efficient inventory management is a crucial aspect of logistics that directly impacts the bottom line of businesses. Packaging plays a key role in optimizing storage, transportation, and overall stock control. Innovations in packaging have the potential to enhance the accuracy and speed of inventory processes, reducing waste and minimizing errors. Companies can leverage new materials, designs, and technologies to improve inventory flow while cutting down operational costs.
By adopting smarter packaging solutions, businesses can not only ensure the safe transport of goods but also create a more organized and scalable inventory system. These packaging innovations contribute to reducing the physical space required for storage and facilitate easier tracking through automation. As a result, the need for manual stock taking is diminished, and businesses can achieve higher levels of efficiency in their supply chains.
Benefits of Packaging Innovations for Inventory Management
- Space Efficiency: New packaging designs maximize storage density, reducing warehouse space usage and allowing for better stock organization.
- Automated Tracking: Advanced packaging incorporates QR codes or RFID tags, enabling automated stock tracking and improving accuracy in inventory counts.
- Reduced Damages: Enhanced protective materials minimize the risk of product damage during transit and storage, decreasing returns and associated costs.
Example: Companies using modular packaging solutions can stack and store items more efficiently, optimizing warehouse layouts. In addition, digital labeling with RFID tags enables real-time updates of stock levels across multiple locations.
Packaging innovation not only contributes to inventory management but also ensures faster decision-making in logistics operations, leading to increased profitability.
Examples of Packaging Solutions Enhancing Inventory Systems
Packaging Type | Impact on Inventory Management |
---|---|
Smart Packaging with RFID | Real-time tracking of goods, reducing stockouts and overstocking |
Modular Packaging | Maximizes storage space and improves warehouse efficiency |
Eco-friendly Materials | Reduces waste and lowers the environmental impact of inventory handling |