Traffic Signal Preventive Maintenance Checklist
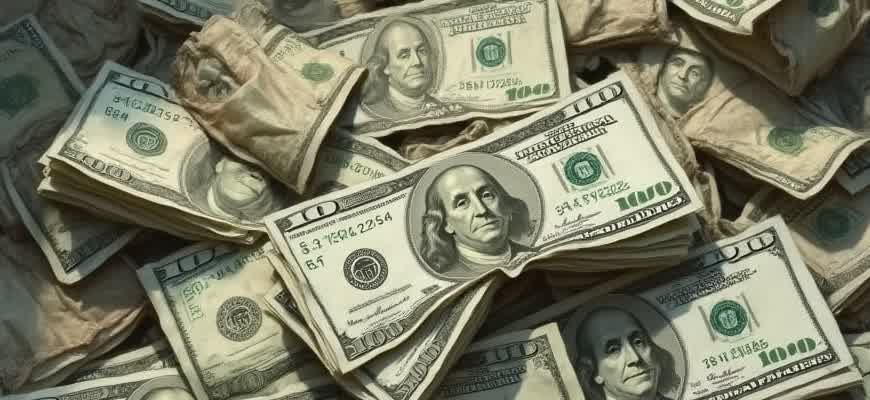
Regular upkeep of traffic control devices is essential to ensure smooth traffic flow and safety on the roads. A detailed preventive maintenance routine helps identify potential issues before they disrupt traffic operations. Below is a recommended checklist for maintaining traffic signals, organized into key areas of inspection.
Inspection of Signal Heads
- Check for any physical damage or signs of wear.
- Verify proper alignment of signal heads for clear visibility.
- Ensure lens cleanliness and replace damaged lenses.
- Inspect for any obstruction in signal visibility such as foliage or dirt.
Electrical System Inspection
- Test voltage levels to ensure consistent operation.
- Check for any loose or corroded connections in wiring and panels.
- Inspect backup power supply systems (e.g., batteries, generators).
Important: Timely replacement of worn-out bulbs and damaged wiring is crucial for maintaining signal functionality, especially in adverse weather conditions.
Controller and Software Maintenance
Task | Action |
---|---|
Signal Timing | Review and adjust signal timing to optimize traffic flow. |
Software Updates | Ensure the controller software is up-to-date with the latest patches. |
Inspecting Traffic Signal Hardware: Key Components to Check
Regular inspection of traffic signal components is essential for ensuring their proper functionality and minimizing the risk of failures. Traffic signals are composed of several key hardware elements, each of which requires periodic checks to maintain optimal performance. This checklist serves as a guide to help identify potential issues before they disrupt traffic flow.
Effective maintenance begins with a thorough examination of critical signal hardware. Regular monitoring of signal lights, controllers, and power systems can prevent malfunctioning and ensure the safety of road users. Below is a breakdown of the components that should be inspected and maintained.
Key Hardware Elements to Inspect
- Signal Heads - Ensure that all lights function correctly and are properly aligned. Check for cracked or damaged lenses.
- Controllers - Verify that controllers are receiving power and communicating with the signal heads. Look for any malfunctions in timing or configuration.
- Power Supply - Inspect the electrical wiring and connections for wear, corrosion, or loose connections. Confirm the voltage is stable and within acceptable limits.
- Detection Equipment - Test loop sensors, cameras, or radar-based systems to confirm they are detecting vehicles accurately and triggering the signals as expected.
- Mounting Structures - Inspect poles, brackets, and other mounting systems for rust, damage, or structural instability. Tighten any loose bolts or screws.
Inspection Process Steps
- Start with a visual inspection of all signal heads, checking for signs of damage or wear.
- Ensure that signal lights are illuminated at the correct intensity, and adjust them if necessary.
- Test the controller for communication with all connected components and ensure it's operating within specified parameters.
- Check all electrical wiring, focusing on connections at the power supply and controller. Replace damaged wires promptly.
- Inspect detection devices for proper vehicle detection and calibration, adjusting as needed.
- Assess the physical stability of mounting structures and reinforce or replace parts as required.
Important Considerations
Regularly updating software and firmware in controllers can significantly reduce issues caused by outdated programming and ensure the system operates at peak efficiency.
Additional Checklist
Component | Inspection Item | Action if Fault Detected |
---|---|---|
Signal Lights | Check for broken or dim lights | Replace or clean lenses |
Controller | Verify signal timing and functionality | Reprogram or replace controller |
Power Supply | Check voltage and connections | Fix wiring or replace power unit |
Detection Equipment | Verify vehicle detection accuracy | Calibrate or replace sensors |
Mounting Structures | Check for rust or loose parts | Tighten bolts or replace damaged structures |
Verifying Signal Timing and Cycle Durations for Optimal Flow
Proper traffic signal timing and cycle management are crucial for maintaining smooth traffic flow and reducing congestion. Timely adjustments based on traffic volume and patterns help to ensure efficient movement of vehicles and pedestrians. Regular verification of signal cycles ensures that the light phases are set to provide the best possible throughput without causing unnecessary delays. This requires an in-depth understanding of the area's traffic characteristics, and regular checks to adjust to changes in traffic patterns, construction, or road usage.
To achieve optimal traffic flow, it's necessary to verify that signal timing corresponds accurately to real-time traffic demand. Factors such as peak and off-peak hours, seasonal fluctuations, and nearby events should be factored into the adjustments. By keeping signal cycles optimized, cities can not only reduce wait times but also enhance road safety and decrease overall emissions from idling vehicles.
Key Steps in Verifying Signal Timing
- Evaluate traffic volumes: Gather data on traffic counts and identify the volume during peak and off-peak hours.
- Adjust green times: Ensure green light durations are appropriate for traffic volume, preventing excessive waiting times.
- Review cycle lengths: Cycle times should align with traffic flow patterns, not too short to cause delays or too long to waste time.
- Pedestrian considerations: Ensure pedestrian light phases are in sync with vehicle signals, without unnecessary wait times.
Steps to Adjust Signal Timing and Cycles
- Collect real-time traffic data via sensors or manual counting methods.
- Analyze patterns to identify congestion points and underutilized signals.
- Adjust signal durations based on the current demand for each direction of traffic flow.
- Ensure pedestrian signals are in harmony with vehicle timings to avoid conflicts.
- Test changes for a set period, monitor results, and refine settings based on feedback.
Important Considerations
Note: Adjusting signal timing based solely on average traffic conditions may not be sufficient. Variability in traffic flow, caused by factors such as roadwork or accidents, requires continuous monitoring and periodic adjustments.
Time of Day | Optimal Cycle Time | Key Considerations |
---|---|---|
Morning Peak (7:00 AM - 9:00 AM) | 90-120 seconds | Increased traffic volume, prioritize major roadways. |
Midday (12:00 PM - 2:00 PM) | 60-90 seconds | Moderate traffic, adjust green time to reduce idle periods. |
Evening Peak (4:30 PM - 6:30 PM) | 120-150 seconds | Higher traffic, consider pedestrian traffic and bus stops. |
Monitoring Power Supply and Backup Systems for Reliability
Ensuring the continuous operation of traffic signals requires consistent monitoring of power systems. Any disruptions in the power supply can lead to signal failures, posing risks to traffic safety. Regular inspections of power inputs and backup mechanisms are essential to prevent unexpected downtime. This includes verifying the stability of main power connections and ensuring that backup generators or battery systems are ready to take over if the primary source is interrupted.
Regular checks and preventive measures will help ensure that traffic signals remain operational during power outages, especially in critical areas. This involves inspecting components like voltage regulators, circuit breakers, and backup power units. Through scheduled monitoring, potential issues can be detected early, minimizing the chance of failure during peak traffic periods.
Key Power Supply and Backup Systems Checks
- Verify voltage stability and ensure no significant fluctuations are present in the main power supply.
- Inspect backup power sources, such as batteries and generators, for charge levels and operational readiness.
- Ensure backup systems automatically activate when the primary power supply fails.
- Test the functionality of transfer switches to confirm smooth transition between power sources.
- Check for any wear or damage in power cables and connections that could disrupt signal performance.
Important Actions for Backup System Testing
- Conduct a full-load test on backup generators once a month to ensure they are operational under real conditions.
- Inspect battery banks at least quarterly for corrosion, leakage, or weak cells.
- Replace backup components that have surpassed their service life to avoid unexpected failures.
Regular monitoring and maintenance of power and backup systems help reduce the likelihood of downtime, ensuring that traffic signals function smoothly even during power interruptions.
Backup System Components Overview
Component | Action | Frequency |
---|---|---|
Power Supply Connections | Inspect for stability and proper connection | Monthly |
Battery Bank | Test charge levels and check for corrosion | Quarterly |
Generator | Run full-load tests and check fuel levels | Monthly |
Cleaning and Maintaining Signal Lenses for Maximum Visibility
Regular upkeep of traffic signal lenses is crucial for ensuring optimal visibility and proper functioning of traffic control systems. Over time, lenses may accumulate dirt, debris, and environmental pollutants that can obstruct light transmission. This can lead to reduced visibility, especially in adverse weather conditions, and may impair traffic safety. Therefore, proper cleaning and maintenance practices must be followed to ensure that the signal lenses remain clear and efficient in their performance.
Maintenance should not only focus on cleaning but also on ensuring that the lenses are free from any cracks or physical damage that could compromise their effectiveness. Inspections should be carried out at regular intervals to prevent issues that may go unnoticed during routine operations. The following steps outline the process for maintaining signal lenses for maximum performance and safety.
Key Steps for Cleaning and Maintaining Signal Lenses
- Inspection: Before cleaning, inspect the lenses for cracks, chips, or any signs of physical damage. Replace any damaged lenses immediately.
- Cleaning: Use a soft, non-abrasive cloth or sponge to clean the lenses. Avoid harsh chemicals that could cause discoloration or damage to the lens material.
- Cleaning Solution: For tough stains, use a mild soap solution mixed with water. Ensure all residues are thoroughly rinsed off.
- Drying: After cleaning, dry the lenses with a clean, dry cloth to prevent water spots or streaks from forming.
- Protective Coating: Apply a protective coating or polish recommended for traffic signal lenses to maintain their clarity and reduce future buildup of dirt and grime.
Maintenance Checklist for Signal Lenses
Task | Frequency | Notes |
---|---|---|
Visual Inspection | Monthly | Look for cracks, discoloration, and physical damage. |
Cleaning Lenses | Quarterly | Use a soft cloth with a mild detergent solution. |
Lens Replacement | As Needed | Replace damaged lenses immediately to maintain visibility. |
Important: Never use abrasive materials or harsh chemicals on signal lenses as they can damage the surface and decrease the lens's effectiveness.
Testing Pedestrian Signals and Push Buttons for Proper Functioning
Ensuring the proper operation of pedestrian signals and push buttons is crucial for maintaining traffic safety. Regular checks should be performed to confirm that both the signals and buttons are functioning as designed. This includes verifying that the signal changes occur in a timely manner and that the push buttons correctly trigger the pedestrian walk phase when pressed. Malfunctions can lead to safety hazards and confusion for both pedestrians and drivers.
Preventive maintenance procedures for pedestrian signals and push buttons focus on checking signal visibility, button responsiveness, and correct timing. These steps should be carried out during routine inspections to prevent potential delays in signal transitions or malfunctioning of the push buttons. Properly working signals help ensure that pedestrians are given adequate time to cross streets, while well-maintained push buttons ensure that the system operates efficiently.
Key Maintenance Tasks
- Signal Visibility: Ensure that the pedestrian signals are clearly visible from all pedestrian approaches and not obstructed by trees, signs, or other objects.
- Button Response: Test the push buttons to ensure they register a signal when pressed. This can be done by checking for a sound or visual indication that the button has been activated.
- Timing Consistency: Confirm that the walk signal is provided for an adequate amount of time based on pedestrian traffic and crossing distances.
Testing Procedure
- Inspect the physical condition of the pedestrian signal heads and ensure they are not cracked or faded.
- Press each push button to verify it triggers the correct signal and provides proper feedback (sound or light). If no feedback is received, further investigation is required.
- Monitor the timing of the pedestrian walk signal to ensure it allows sufficient time for pedestrians to cross safely.
- Check the coordination of signals with other traffic signals to avoid unnecessary delays or unsafe pedestrian movement.
Important Notes
Note: Always document the results of the tests, including any malfunctions or required repairs. This helps track maintenance progress and ensures that any issues are addressed promptly.
Common Issues
Issue | Possible Cause | Solution |
---|---|---|
Unresponsive Push Button | Worn-out or malfunctioning button | Replace the button or repair the wiring |
Delayed Signal Change | Incorrect signal timing or controller malfunction | Adjust the signal timing or replace the controller |
Obstructed Pedestrian Signal | Physical obstruction like signs or vegetation | Remove the obstruction or relocate the signal |
Ensuring Proper Signal Placement and Alignment
Accurate positioning and alignment of traffic signals are essential for their effectiveness in guiding traffic flow and ensuring safety. Improper placement or misalignment can cause confusion for drivers, potentially leading to accidents or traffic violations. During preventive maintenance, it's crucial to verify that signals are correctly located at intersections, in clear view of approaching vehicles, and at the optimal height for visibility.
Signal alignment must be checked periodically to ensure they are properly oriented towards oncoming traffic. Misalignment due to factors such as weather, wear and tear, or accidental impacts can diminish the effectiveness of the signals. Regular inspections and timely adjustments help in minimizing the risks associated with poor signal visibility or miscommunication.
- Check signal placement at intersection points for maximum visibility.
- Ensure signals are not obstructed by trees, poles, or other structures.
- Verify that signal heads are positioned at the correct height according to local regulations.
- Ensure that signals are not tilted or turned away from oncoming traffic.
Important: Proper signal placement must account for sight distance and clearance from obstructions to avoid visual distractions.
- Inspect signal heads for proper tilt and horizontal alignment.
- Assess the distance between signals to ensure adequate spacing for clear visibility.
- Check that signal faces are visible from all lanes of traffic.
Condition | Action Required |
---|---|
Signal misalignment | Realign to ensure proper angle towards traffic flow. |
Obstructed signals | Clear obstruction or reposition signal head. |
Improper signal height | Adjust height according to standard guidelines. |
Reviewing Traffic Signal Controllers and Software Updates
Maintaining traffic signal controllers in optimal condition is critical for ensuring smooth traffic flow and minimizing downtime. One of the key aspects of this process is the regular review of controller systems, which includes checking the hardware components and ensuring that the software is up-to-date. Software updates are essential for improving system performance, enhancing security, and introducing new features that address evolving traffic management needs.
Regularly updating the controller software helps prevent compatibility issues, enhances communication between signal components, and ensures that the system adheres to the latest standards and protocols. Without these updates, controllers may become prone to malfunctioning or fail to integrate with newer traffic management technologies.
Key Steps for Reviewing Controllers and Updates
- Hardware Check: Inspecting controllers for physical damage or wear and tear.
- Firmware Version Review: Ensuring that the firmware is up-to-date with the latest updates provided by the manufacturer.
- Configuration Validation: Verifying that the controller settings align with current traffic management requirements.
- Software Patch Updates: Installing security patches and software updates to address vulnerabilities.
- Testing Post-Update: Conducting post-update tests to confirm that all functions are working correctly.
It is crucial to stay ahead of software vulnerabilities by regularly updating controllers to avoid security risks and ensure uninterrupted traffic management.
Update Schedule and Record Keeping
- Review and update controller firmware every six months or as recommended by the manufacturer.
- Keep a log of all updates, including date, version, and changes made.
- Verify system functionality immediately after updates to confirm proper operation.
- Schedule routine checks to ensure that software updates do not conflict with existing traffic control systems.
Action | Frequency | Notes |
---|---|---|
Hardware Inspection | Quarterly | Check for physical damage or malfunctions. |
Firmware Update | Every 6 months | Ensure compatibility with other traffic management systems. |
Software Patch Installation | As needed | Install patches as soon as they are released to address vulnerabilities. |
Documenting and Reporting Maintenance Activities and Issues
Proper documentation and accurate reporting of traffic signal maintenance activities are essential for maintaining safety and system reliability. These records provide a comprehensive history of inspections, repairs, and any issues encountered, which are crucial for future planning, troubleshooting, and compliance with regulatory requirements. Ensuring that every action is logged with clear details allows for effective follow-up and accountability, ensuring that no issues are overlooked or unresolved.
Effective reporting should capture the full scope of maintenance work performed, including both scheduled checks and unscheduled repairs. Each report should be organized in a structured format, which enables easy tracking of patterns or recurring problems. Proper documentation ensures that the team remains informed about the current state of each intersection and facilitates the identification of long-term trends in signal functionality.
Key Elements of Maintenance Documentation
- Date and Time: Record the specific date and time of each maintenance task or inspection.
- Location: Identify the exact intersection or signal location where the work was performed.
- Tasks Performed: List detailed actions taken, such as bulb replacements, wiring checks, or software updates.
- Issues Identified: Note any malfunctions, wear, or damage found during inspections or repairs.
- Actions Taken: Specify the repairs or preventive measures applied to address the identified issues.
Maintenance Reporting Procedures
When submitting maintenance reports, it is important to adhere to a consistent format. This can help identify recurring problems, prioritize future work, and improve operational efficiency.
- Initial Review: Inspect the traffic signal and document any visible or functional issues.
- Reporting: Enter the detailed findings into the system with precise descriptions.
- Follow-up Actions: Ensure that any unresolved issues are flagged for further action and assigned to the appropriate personnel.
- Feedback: Provide recommendations for future inspections or upgrades if necessary.
Important: Consistent and detailed reporting not only enhances system performance but also supports compliance with industry standards and safety regulations.
Example of a Maintenance Report
Date | Location | Issues Identified | Actions Taken |
---|---|---|---|
April 12, 2025 | Intersection A | Flickering traffic light | Replaced faulty bulb and recalibrated signal timing. |
April 13, 2025 | Intersection B | Signal not responding to pedestrian request | Checked wiring, replaced faulty sensor. |