Slow Traffic Ahead Sign
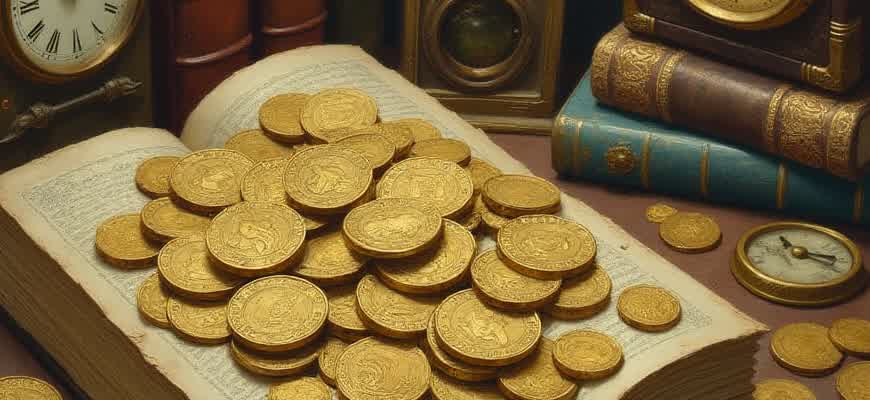
Motorists frequently encounter roadway alerts that signal a reduction in vehicle flow ahead. These notices are critical for ensuring driver preparedness in areas prone to congestion due to construction, merging lanes, or sudden changes in terrain. A few key characteristics of these notifications include:
- Bold, high-contrast lettering for maximum visibility
- Strategic placement before bottlenecks or work zones
- Often accompanied by additional signage indicating distance or cause
Drivers are required to reduce speed and remain alert when approaching these signals to ensure safety for themselves and others.
The importance of these alerts is especially evident in high-risk zones. They serve not just as warnings, but as legally enforceable directives. Failure to comply may result in fines or legal penalties. Consider the following common causes for reduced speed notifications:
- Road construction or maintenance
- Accidents or emergency response activity
- Narrow lanes or temporary detours
Cause | Driver Action |
---|---|
Ongoing Construction | Merge early and reduce speed |
Lane Closure | Stay in designated lane and follow arrows |
Accident Scene | Proceed cautiously, watch for emergency crews |
Choosing the Right Material for Durability in Different Weather Conditions
Outdoor signage exposed to varying environmental factors must be crafted from materials that ensure visibility and longevity. When selecting the construction for cautionary road indicators, it's essential to assess resistance to UV radiation, precipitation, and temperature fluctuations. Materials not optimized for these conditions may fade, crack, or become illegible over time.
Effective performance in extreme climates–whether arid heat or coastal humidity–requires selecting substrates and finishes that provide specific protective properties. This ensures that warning messages remain clear and intact, even under heavy wear and harsh weather exposure.
Weather-Resistant Signage Options
- Aluminum: Lightweight, rustproof, and ideal for humid and coastal regions.
- High-Density Polyethylene (HDPE): Resists impact, moisture, and UV degradation.
- Engineer Grade Reflective Sheeting: Enhances nighttime visibility while withstanding rain and sun exposure.
Note: In regions with frequent snowfall or intense sun, UV-resistant coatings and anti-fade treatments are critical for maintaining visibility.
- Evaluate local climate zones (heat, frost, humidity).
- Choose corrosion-resistant bases (e.g., powder-coated aluminum).
- Use reflective surfaces meeting MUTCD standards for visibility.
Material | Best For | Weaknesses |
---|---|---|
Aluminum | Rain, snow, coastal air | Dents under impact |
HDPE | Cold climates, high impact zones | Lower reflectivity |
Fiberglass | Windy or high-vibration areas | UV sensitivity if uncoated |
Standard Sizes and Reflectivity Grades: What You Need to Know
Traffic signs warning of reduced vehicle speed requirements must meet specific dimensional and visibility standards to ensure driver compliance. Dimensions are not arbitrary–they're set based on the placement and expected speed of approaching vehicles.
The reflective coating on signs directly influences nighttime visibility and compliance. Choosing the correct grade ensures the sign remains effective in various lighting and weather conditions.
Dimensions by Application
- 24" x 24" – Recommended for low-speed urban environments.
- 30" x 30" – Common on local and collector roads.
- 36" x 36" – Suitable for highways or areas with higher speed limits.
Signs placed on roads with speed limits above 40 mph should not be smaller than 30" x 30", according to MUTCD recommendations.
Reflective Sheeting Grades
Grade | Visibility Range | Common Use |
---|---|---|
Engineer Grade | Up to 500 ft | Private roads, parking areas |
High Intensity Prismatic | Up to 1,000 ft | City streets, suburban areas |
Diamond Grade | Over 1,000 ft | Highways, critical safety zones |
- Engineer Grade is budget-friendly but has limited visibility.
- High Intensity provides good visibility for most urban and rural applications.
- Diamond Grade is required for high-risk or high-speed traffic environments.
For maximum safety, always align the reflectivity grade with the road type and ambient lighting conditions.
Compliance with Federal and Local Road Sign Regulations
Ensuring traffic signage meets both national and municipal guidelines is essential for legal enforcement and driver safety. Regulatory consistency prevents confusion among drivers and supports uniform traffic control measures across different jurisdictions. Each warning sign, including those indicating reduced traffic speeds, must align with established standards to remain effective and lawful.
All traffic control devices must comply with the Manual on Uniform Traffic Control Devices (MUTCD), which outlines the design, placement, and application of roadway signs. Local authorities may introduce additional specifications, but these must not conflict with the federal standards. Coordination between agencies is crucial to maintain clarity and compliance on public roads.
Key Requirements for Road Sign Approval
- Adherence to MUTCD sign formats and colors
- Verification of sign visibility at designated distances
- Use of retroreflective materials for nighttime readability
- Local transportation departments review site-specific conditions
- Approval processes ensure non-standard signs meet safety criteria
- Inspection schedules confirm ongoing compliance
All signage on public roadways must be legible, recognizable, and interpretable under various environmental and lighting conditions.
Regulation Level | Responsible Authority | Primary Focus |
---|---|---|
Federal (MUTCD) | Federal Highway Administration | Standardization of sign design and usage |
Local | City or County Traffic Engineers | Application to local traffic scenarios |
Mounting Options and Placement Tips for Optimal Visibility
Correct installation of reduced-speed warning panels ensures drivers have ample time to respond to upcoming road conditions. Choosing the right mounting method depends on the location, environment, and intended duration of use. Permanent and temporary installations require different hardware and placement logic to maintain maximum effectiveness.
Improper positioning can lead to reduced awareness and increased risk. It's critical to account for sightlines, road curvature, and driver reaction time when determining sign location. Consistent height and angle alignment with other regulatory signs also improves readability and compliance.
Recommended Mounting Methods
- U-Channel Posts: Durable and commonly used for roadside placement along highways and rural roads.
- Portable Sign Stands: Ideal for short-term use in construction or maintenance zones.
- Wall or Fence Mounting: Suitable for controlled environments like parking lots or industrial areas.
Important: All installations should withstand wind loads as specified by local transportation standards.
Ideal Placement Guidelines
- Ensure a minimum clearance of 5 feet from the bottom of the sign to the ground in urban settings.
- Place signs at least 500 feet before the area of reduced speed or obstruction for highway use.
- Position signs on the right-hand side of the road unless additional visibility is needed on the left or center median.
Environment | Mounting Height | Minimum Distance from Hazard |
---|---|---|
Urban Streets | 5–7 ft | 150 ft |
Highways | 7 ft | 500 ft |
Construction Zones | Portable (varies) | 100–300 ft |
Maintenance Practices to Preserve Visibility Over Time
Ensuring that roadside warning indicators remain clear and legible requires consistent upkeep. Environmental factors such as UV exposure, dirt accumulation, and physical wear can significantly reduce reflectivity and color contrast, making signs harder to read for drivers. Regular inspections and targeted interventions can prevent such degradation.
Fading, peeling, or obscured messages can compromise safety. To maintain high visibility, a structured maintenance schedule and precise cleaning protocols are essential. Materials used in the signage, installation angle, and proximity to vegetation or road debris all influence how often servicing is needed.
Key Maintenance Procedures
- Monthly Visual Inspections: Detect cracks, discoloration, or graffiti.
- Bi-Annual Cleaning: Use soft brushes and non-abrasive detergents to remove dirt, pollen, and smog residue.
- Annual Reflectivity Testing: Utilize retroreflectometers to assess nighttime visibility.
- Vegetation Control: Trim surrounding foliage that may block visibility.
Note: Signs positioned near intersections or curves may require more frequent checks due to increased wear and critical visibility demands.
Task | Frequency | Responsible Party |
---|---|---|
Surface Cleaning | Every 6 months | Maintenance Crew |
Visibility Assessment | Quarterly | Traffic Safety Officer |
Component Replacement | As Needed | Signage Contractor |
- Establish inspection logs to track condition changes over time.
- Prioritize high-risk areas based on traffic volume and incident data.
- Implement a replacement cycle for signs exceeding five years in service.
Common Mistakes to Avoid When Installing Warning Signs
Incorrect placement of traffic caution indicators can significantly reduce their effectiveness, leading to potential hazards. Ensuring visibility, relevance, and compliance with safety standards is critical when setting up such signs in any roadwork or slow zone area.
Many installation errors stem from poor judgment in location, height, and orientation. These mistakes not only compromise the safety of drivers and pedestrians but may also result in legal consequences for the responsible parties.
Installation Pitfalls to Watch Out For
- Obstructed Visibility: Placing signs behind trees, utility poles, or parked vehicles reduces their function.
- Incorrect Height: Signs too low or too high can be missed by approaching drivers, especially in poor weather.
- Wrong Distance: Warning signs placed too close to the hazard leave insufficient time for driver response.
- Poor Contrast or Faded Print: Weathered or low-contrast signs are difficult to read, particularly at night.
Important: A warning sign must be visible from a minimum distance of 500 feet in rural settings and 250 feet in urban areas.
- Assess the environment and traffic flow before installation.
- Use certified signs with high-reflectivity materials.
- Check local and federal regulations for placement guidelines.
- Conduct visibility tests under different lighting conditions.
Mistake | Consequence |
---|---|
Placed after the hazard | No preventive action possible |
Improper mounting angle | Drivers may not see the sign at all |
Unclear wording or symbols | Delayed reaction or confusion |
Bulk Ordering, Customization, and Vendor Comparison Checklist
When planning to purchase "Slow Traffic Ahead" signs in bulk, it’s important to assess several key factors that could influence your decision. Ordering in large quantities can lead to significant cost savings, but you must ensure that customization options are available to meet your specific needs. Additionally, comparing different suppliers is essential to finding the most reliable option for your requirements.
The following checklist can guide you through the process of bulk ordering, ensuring the customization of your signs, and comparing vendors effectively. By evaluating all aspects carefully, you can make a well-informed decision that satisfies both your budget and functional needs.
Checklist for Bulk Ordering and Customization
- Quantity Discounts: Ensure that the supplier offers discounts for large orders.
- Customization Options: Look for the ability to adjust text, graphics, or colors on the signs.
- Material Choices: Consider weather-resistant materials that are suitable for outdoor use.
- Compliance with Standards: Verify that the signs meet local road safety regulations.
- Delivery Timeframes: Ensure the supplier can meet your required delivery date.
Vendor Comparison Table
Vendor | Customization Options | Bulk Pricing | Delivery Time |
---|---|---|---|
Vendor A | Text, Color, Graphic Changes | 10% off for orders over 50 units | 3-4 weeks |
Vendor B | Text, Material Customization | 15% off for orders over 100 units | 2-3 weeks |
Vendor C | Graphic Customization Only | 5% off for orders over 30 units | 4-6 weeks |
Tip: Always request a sample before placing a large order to verify quality and customization accuracy.
Vendor Evaluation Criteria
- Reputation: Research customer reviews and feedback on reliability and product quality.
- Certifications: Ensure the vendor complies with relevant traffic sign safety standards.
- Warranty: Look for vendors that offer product warranties or guarantees for peace of mind.